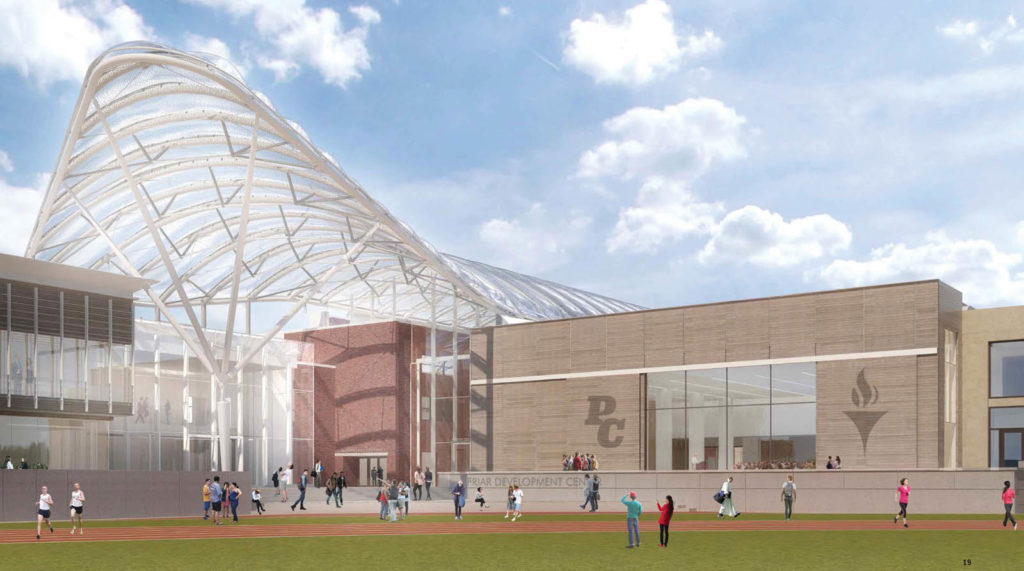
More than ever before, architects are being called upon to dramatically improve the performance of their buildings, and fabric can help with this mandate. The key to implementing this is to reduce the embodied carbon in buildings.
It’s a given that 40 percent of global resources goes to the built environment, so our construction industry must significantly ameliorate this problem. Embodied carbon can come from either direct building contributions or operations. Building contributions include products, transportation to site, construction and maintenance. Operations includes heating and cooling, lighting and power. How can the fabric structures industry address these two issues to become more sustainable?
This is the takeaway message I gleaned from a trio of experts who recently gathered to discuss the importance of fabric in the battle to reduce the carbon footprints of all construction, but especially lightweight buildings. Nicholas Goldsmith, Denis Hector and Marc Shellshear spoke with me about the urgent need to find solutions to the impact of global climate change, the apparent increase of disasters from natural causes, and a universal societal need for reliable shelter and reduction of the carbon footprint of buildings.
Architect Goldsmith, FAIA, LEED AP, senior principal at FTL Design Engineering Studio in New York City, whose specialty is designing and engineering tensile membranes, spoke of numerous areas where architects and specialty contractors in this industry can direct their efforts using architectural fabrics, three of which include:
1) Adaptively reusing existing and underused buildings.
2) Developing demountable structures to minimize wastage of building materials and addressing climate refugees.
3) Retrofitting existing buildings to improve thermal efficiency and reduce energy usage.
Adaptive reuse
“Since 40 percent of global resources goes to the built environment and it would take 100 years to rebuild all our buildings sustainably for which we don’t have the time, we need to rethink our approach to building,” Goldsmith says. “Rather than extract more raw materials to build new buildings, we should find new uses for existing structures.”
A great way to do this is using fabric and foils to improve the thermal performance of these buildings.
“This can be done using such things as replacement membrane facade systems or overcladding enclosures using membranes such as ETFE that have a carbon footprint 80 percent lower than glass wall systems. By using these enclosures as primary or secondary building skins, we can improve the thermal envelope of the existing buildings in cold climates or create shading opportunities for passive cooling in hot climates. A current project we are working on, the Ruane Friar Center at Providence College, is an example which ties four existing sport facilities together by adapting a three-layer ETFE foil roof to cover an unused pedestrian street.”
This, Goldsmith says, improves the overall insulation of the older buildings, which were built under older energy codes. “A glass atrium design approach would have been over 50 times heavier and would have required reinforcement of all the existing buildings, making the project unaffordable.”
Demountable shelters
“Not only are demountable fabric structures lighter on the earth, due to lower embedded carbon of the materials used, they also can reduce the operational energy usage, thus reducing operational carbon footprint,” Goldsmith says. “In addition, we are now facing climate disasters monthly, with the U.S. now being the fifth largest country of population displacements caused by climate disasters.” To address this displaced population, Goldsmith predicts we will need relocatable buildings that can be set up quickly and moved as needed. “Some products exist but we need to develop more integrated ones.”
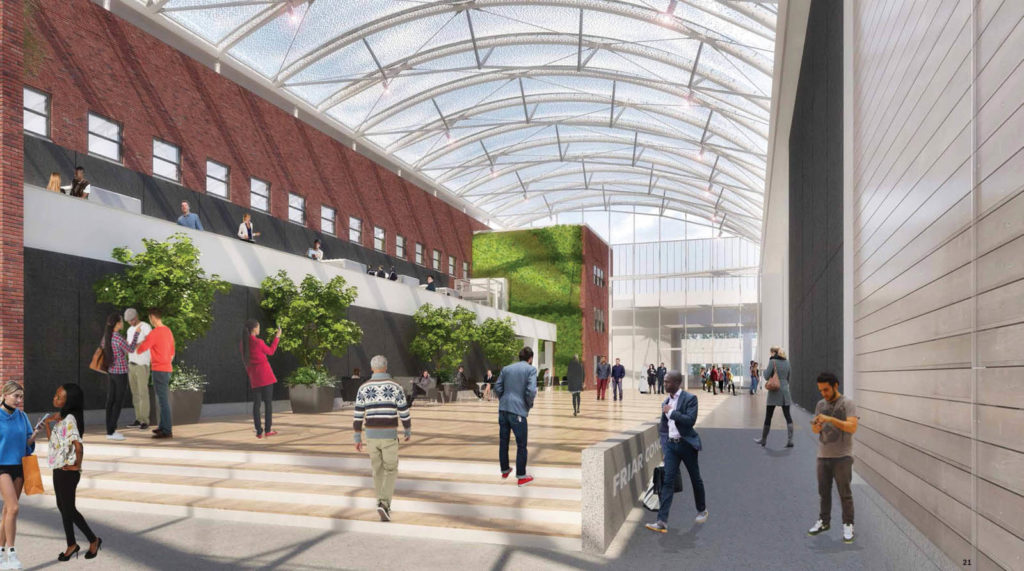
Retrofits to existing buildings
As fabric structures are no longer strange creatures, having been introduced to contemporary architecture in the 1960s by Frei Otto (German Pavilion, Montreal Expo 1967) and the British futurists group Archigram (1960s–1970s), the need to refurbish aging structures becomes another area where architects can help improve performance. Goldsmith shows a creative solution for something as mundane as an unused baseball stadium in Connecticut.
“Fabric structures lend themselves readily to the renovation and reuse of pre-existing structures,” he says. “A recent project of ours nearing completion is the Hartford HealthCare Amphitheater in Bridgeport, Conn., taking an unused minor league baseball stadium to create a music facility. Using the existing foundations that supported the bleachers, a series of columns rise up to support a circular compression truss that holds up a new fabric roof. The roof is extended upward using a center flying mast that works on the principle of tensegrity forces, leaving the performance space below free of all supports that might intrude on sightlines.”
LEED by design
Shellshear, IFM, MFC, general manager for Value Vinyls Inc., understands the importance of working with architects when specifying building materials.
“When it comes to LEED issues in the fabric structures arena, it is extremely important to make sure that any fabricator you use can verify their [Environmental Product Declarations] and sources of their raw materials as well as the sustainability of their fabrication processes,” he says. Key questions to ask, says Shellshear: Can they quantify and document their recycling of production waste? Can they prove that the fabric manufacturer has the certifications? “There is no quicker way to get a product tossed out of specifications than to claim LEED and not be able to support the claim.”
Return on investment
While most building types are regularly valued according to the market, fabric structures are rare enough that many designers have little experience in pricing. Anything more than a small-scale shade element—in other words a major fabric structure—will induce sticker shock to the unfamiliar.
“As architects, you can help sell your client on the value and cost of a fabric structure via ROI,” says Shellshear. “A simple, but effective example would be adding a fabric structure to a restaurant to allow them to keep functioning during pandemic restrictions. Begin by collecting the following data on your client: (A) When are they open? (B) Is this lunch versus dinner sales? (C) What additional number of seats/tables could be added if this shelter were built? (D) What positive visual impressions would customers gain by sitting outdoors under shelter?”
Add up the numbers, Shellshear says. For example, if it will be open seven days a week 11 a.m. to 11 p.m.? Lunch versus dinner sales? 35% (lunch) versus 65% (dinner)? Number of seats/tables added: 40/10? Visual perceptions: open beach views? Pool? Or main street?
Then, convert this to dollars, as in this example provided by Shellshear: Part B: $14 (lunch) versus $29 (dinner) average cost per person meal charged. $14 X 40 additional tables X 1.5 average number of people/table: 14 X 40 X 1.5 = $840. For dinner the numbers are: $29 X 40 X 3 people/table = $3,480. Add these together and this equals an additional $4,320 per day of added sales. At a 25% margin this equals $1,080/day of profit.
For the longevity of a fabric structure, Shellshear suggests an average of 10-plus years. “With the cost of an average small fabric structure for a restaurant at $50,000, this gives you/your client an ROI of 46 days or six weeks. When put in these terms, clients can easily see the value of adding directly to their pocketbooks and contributing to their operating expenses.”
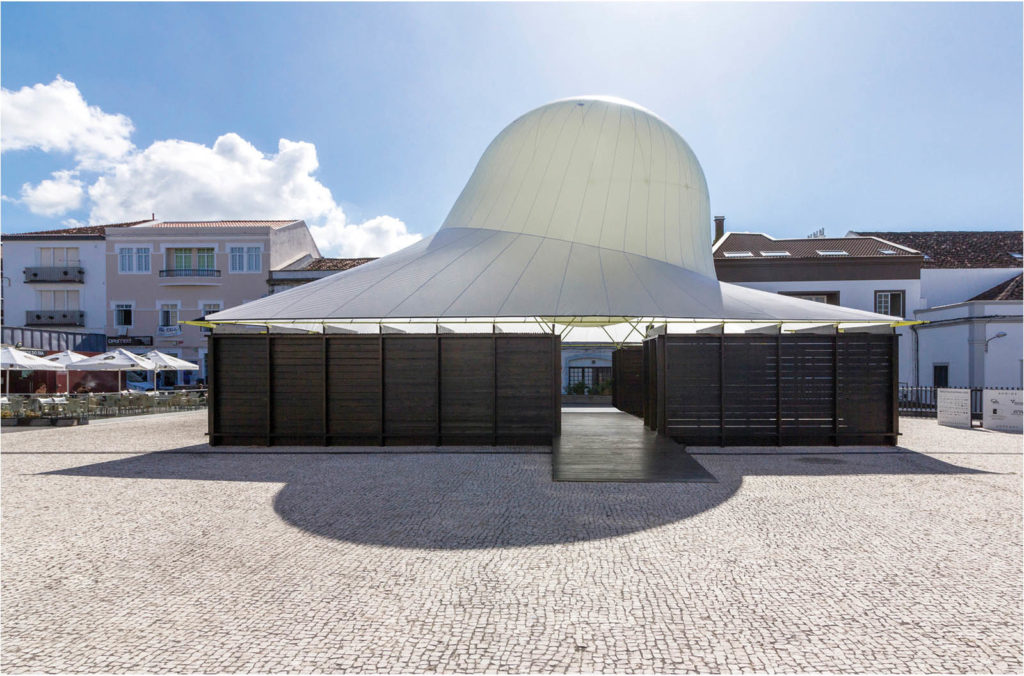
Improvements over time
Hector, RA, LEED AP, associate professor at the University of Miami School of Architecture, Miami, Fla., conducted research at the Institute for Lightweight Structures under Frei Otto in Stuttgart, Germany. With many years of design and project management in fabric structures, he’s seen vast improvements since his start, but feels the need for more sustainable efforts.
“There certainly is a lot to be done, both within the architectural community and the fabric architecture communities,” Hector says. “One area that has shown improvement is between the different players in the fabric architecture field, especially between the designers and the fabricators. In the number of years I’ve been in the fabric structure field, the number of companies and individuals working in this area has grown significantly but not as much as we may have hoped back in the 1970s. It was very exciting at the time and the potential since then has been explored greatly, but there still needs to be more. However, both sides need to learn more from each other. For instance, there is a huge difference in scale between a small fabric structure—such as demountable clearspan tents [as used for weddings or events] and large-scale tensile structures like major sports arenas and stadia. This shows up dramatically in the skill levels required for correctly detailing, and connections, anchoring and the parabolic edge details of fabric in tension.
“Not to scare off any architects, after all there is nothing wrong with being aspirational, but getting the detailing wrong can affect the reputations of everyone in the business. To that end, I feel architects need to hear more from the construction side of things to help improve the outcomes for all concerned.”
Next steps
“What we all need now is more productive sharing between the design, the fabrication and the materials manufacturing groups,” says Hector, “so that a more cohesive and sustainable production can ensue.”
“Fabric is a viable building material, but warranty does not equal longevity,” says Shellshear. “Cheaper is generally for a reason. As a designer, you would want your clients to see the value of hiring you to design their new building or upgrading an existing building. Fabric can be equal to many traditional building materials yet weigh less, can have a lower carbon footprint and can often remain as durable as other types of materials if correctly specified.”
“Climate change can make us change our industry again,” says Goldsmith. “Now is the time; we can do it. What part will you play?”
Bruce N. Wright, FAIA, the former editor of Fabric Architecture, teaches architecture and construction management at Dunwoody College of Technology and is a consultant to architects and designers. He is a frequent contributor to Specialty Fabrics Review and Advanced Textiles Source.
SIDEBAR: Sustainability of materials
Material recycling will be required for all industrial fabrics, as they will need to become carbon neutral and Cradle to Cradle (C2C) Certified®. Cradle to Cradle is a manufacturing process that models nature; all pieces in a product are treated like nutrients that are either upscaled and reused in a new way or returned to the earth. They fall into two categories: either technical or biological. We can use wood instead of steel when possible and recycled aluminum; however, membranes generally today use chlorine and fluorine compounds, which are not sustainable.
There are some greener membrane products like the NovaShield® membranes from Intertape Polymer Group, which are currently C2C certified. Another example is NOWOFOL®’s ETFE foil, which is a homogenous product that can be completely recycled, turning the foil into granular products and then refabricate it as a new foil, helping make NOWOFOL a climate neutral company.
Another fabric manufacturer, Serge Ferrari, developed the Texyloop® system for PVC recycling, closed it in 2018, and is now opening a new system called Polyloop that, rather than be a single location for recycling, has become smaller locations throughout the world giving recycled products an easier path for installers. Ferrari currently has an EPD rating for cradle to grave.
—Nicholas Goldsmith, FAIA, FTL Design Engineering Studio, New York City
SIDEBAR: LEED counts for shade
Fabric shade systems can contribute to a LEED calculation for energy efficiency, materials, quality of environment and other areas of the LEED system. Total points can range from 1 to 18, depending on category and stacking categories.
Categories
ENERGY & ATMOSPHERE
• Required shading devices can optimize energy usage and reduce heat gain and heat island effects.
Keep in mind:
Interior shading combined with low-e glass fenestration can produce 13 percent reduction in heat gain. This assumes SHGC is E Screen 3 percent Charcoal/ Charcoal colors. Different fabrics will have different effects on SHGC percent improvement.
Exterior shading, with standard double pane windows can produce up to 84 percent reduction in heat gain. The key is to stop the sun from hitting the glass or heat will conduct into the interior and then dissipate to inside air, loosing the maximum advantage of a shading system. Maximum efficiency requires fully integrated and automated shading devices that respond actively to changing atmospheric conditions.
MATERIALS & RESOURCES
• Fabric shading materials can count toward Materials & Resource calculations because many fabrics are produced in sustainable ways, and/or made from recycled materials.
• When going for LEED certification, shade fabrics can be submitted for HPD disclosure.*
INTERIOR ENVIRONMENTAL QUALITY
• Thermal comfort can be improved with exterior shading devices and lend individual control of interior spaces.
• Glare reduction can be realized from shading (both interior and exterior) and daylighting control for optimized exterior views.
* The HPD Open Standard is a standard specification—composed of a format and instructions—for the accurate, reliable and consistent reporting of product contents and associated health information, for products used in the built environment. —Health Product Declaration® (HPD) Collaborative
Source for this topic: Draper • www.draperinc.com