Each year, fabricators across the globe set the bar higher by achieving more beauty, functionality and innovation in their shade projects. And each year, the Advanced Textiles Association (formerly IFAI) strives to recognize these industry leaders through its International Achievement Awards (IAA) program. Here, we interview four of last year’s winners about the rewards and challenges they experienced while designing, fabricating and installing these award-winning projects.
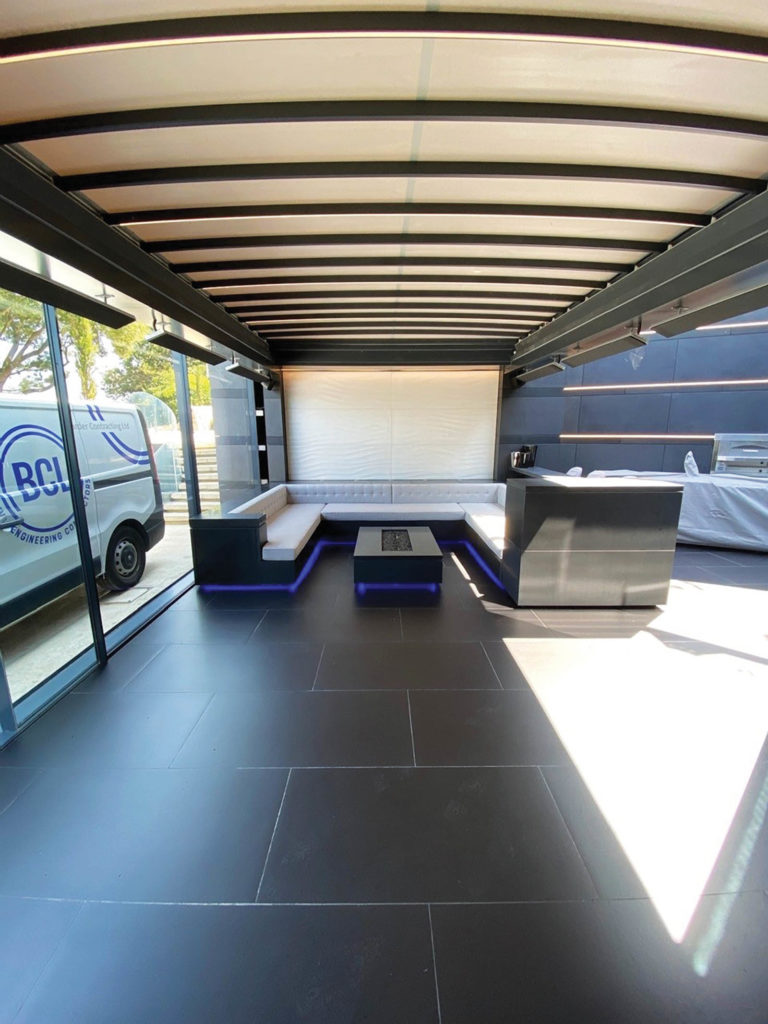
2021 Award of Excellence
Residential Retractable Awnings and Canopies
RetractableAwnings.com Inc., Miami, Fla.
Interviewee: Eric M. Scop, Vice president sales/digital marketing
Project specs: As part of a mansion renovation on the island of Jersey [the largest of the Channel Islands located between England and France], the client wanted a fully enclosed outdoor area for entertaining, featuring a waterproof retractable roof system and sliding glass doors. Project goals included rain protection, shade and protection from harmful UV rays while allowing for the view. Extrusions and assembly components were 6063 aluminum and 316 stainless steel; specs included Soltis® 502 Proof by Serge Ferrari and a 240v Somfy® RTS motor.
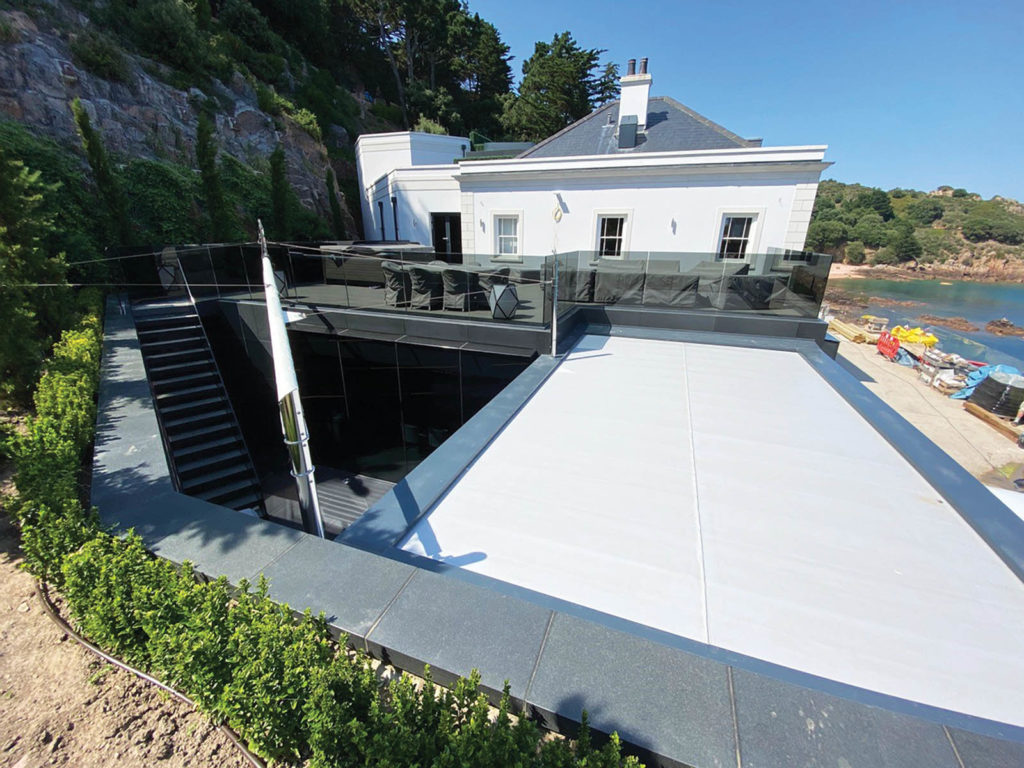
How was this different from past projects? The retractable roof was being installed within a structure built by a third party, so dimensions had to be perfect. They were provided in metric and had to be converted to imperial and back for design and manufacturing. Then the product had to be crated and drop-shipped from our vendor in Europe to the Channel Islands.
What were the unique, challenging and complex facets? The contractor was responsible for building invisible downspouts to drain rainwater away from the structure; our systems typically include internal, invisible rain drainage. And moving the crate from the seaport was difficult because of Jersey’s beaches and cliff trails.
What skills and knowledge were most important to getting this done? Attention to detail was paramount since our system had to fit perfectly and couldn’t be out of spec by even 1 mm.
Advice for fabricators dealing with similar challenges? Product knowledge, attention to detail, and taking time to understand client needs are things we would recommend.
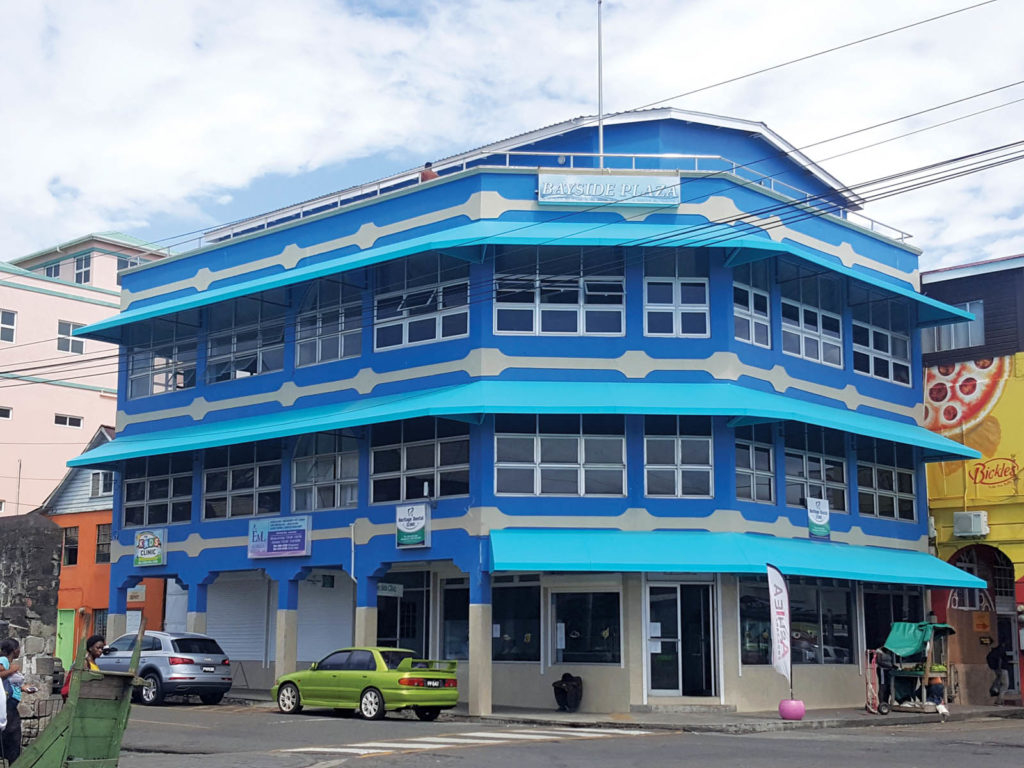
2021 Award of Excellence
Commercial Awnings and Canopies
<93 square meters (1,000 square feet)
Caribbean Awning Production Co. Ltd., St. Lucia
Interviewee: Jonathan Calderon, Accounting, operations and sales manager
Project specs: A three-story building with a frame made in 19 sections, to be bolted and covered on-site, with angles/corners to also be welded and covered on-site. The canopy was 1,775 square feet, with a 60-inch projection and 36-inch drop using Weblon® Coastline Plus® CP-2704 17-ounce turquoise fabric by Herculite Products Inc.
How was this different from past projects? It was an export to the neighboring island of St. Vincent.
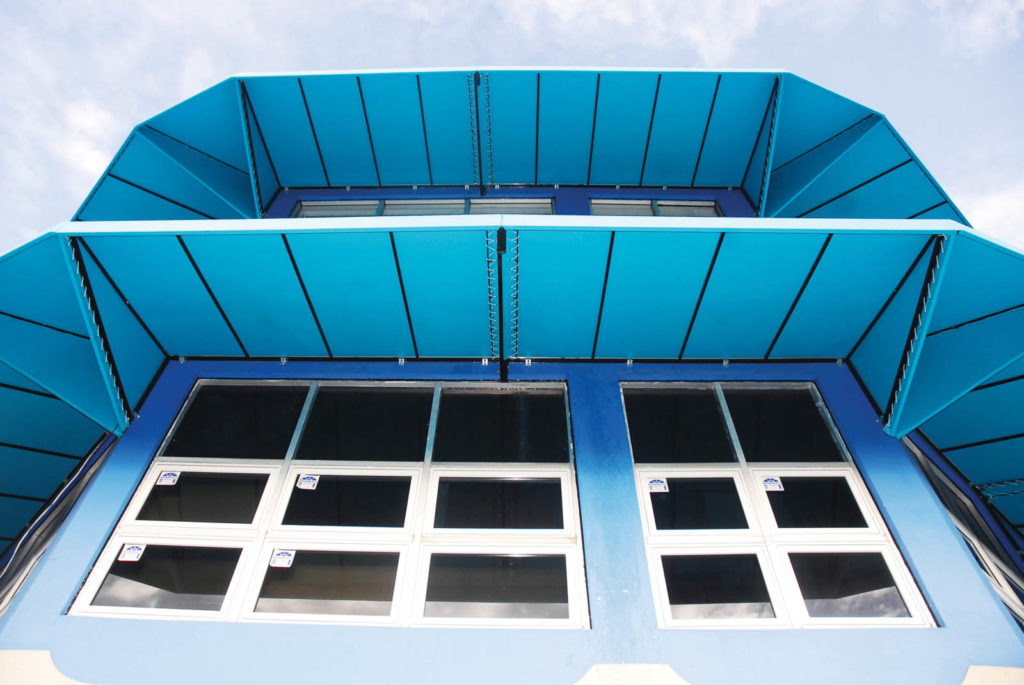
What were the unique, challenging and complex facets?
1. Safely packaging and shipping this large product without damage to the frame or fabric
2. Working with lifts and scaffolding at a three-story building on a busy downtown street
3. Fabricating and shipping the frames and fabric separately and in sections
4. Shipping all tools necessary for completing the job on-site
5. Implementing cost-effective, timely and secure shipping of the fabricated frames and fabric to the island, then coordinating inland transport to the site itself
6. Coordinating transport of the product from our shop to the shipping port to the site with an inland freight/transport team and with the client’s building contractor and engineer
7. Adhering to an 11-day installation period while coordinating daily safety and workflow efficiency, while factoring in building occupancy and street traffic
8. Staying on schedule and under budget in spite of the high cost of hotel stays and per diem fees for the technical staff
What skills and knowledge were most important to getting this done? Adhering to our ISO 9001-2008 production protocols and quality control system was key.
What problems/issues were overcome? The canopy was fabricated using the tie-bar method, using grommets, awning rail, and reel and rope to fasten the fabric to the frame on-site. Instead of riveting the fabric to the frame, we shipped the frames separately from the fabric to avoid damage to an otherwise prefabricated product. We also rented tools on the island due to unforeseen issues with angles and corners that had to be fabricated on-site.
Advice for fabricators dealing with similar challenges? Continually training and practicing ISO and company protocols on a daily basis and on every job prepares your team and entire company for other jobs—no matter the size and scope.
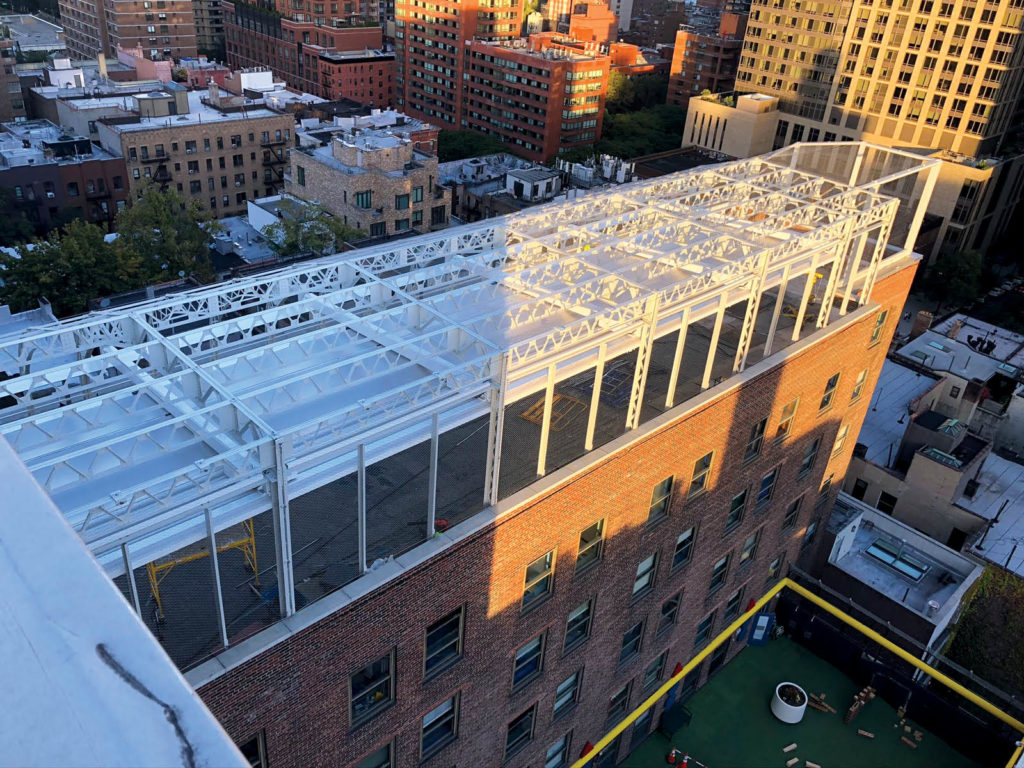
2021 Outstanding Achievement
Commercial Retractable Awnings and Canopies
Uni-Systems LLC, Minneapolis, Minn.
Interviewee: Peter Fervoy, President
Project specs: The project was erected on the rooftop of the historic Manhattan community center 92nd Street Y (otherwise known as 92NY). It applies a custom En-Fold® retractable canopy system using Shelter-Rite® 3820 FRLTC DC-0 Clear by Seaman Corp. to cover an area of 1,826 square feet. The approximately 22-by-82-foot canopy is attached to an existing steel structure to turn the space into a rooftop playground, green space and after-hours event area. It offers shade and weather protection while being completely retractable to comply with city requirements.
How was this different from past projects? It was kind of normal in terms of size, but there were 100-year-old curved, steel-angle trusses we had to use to support the canopy. This original steelwork was built to support chain-link fencing, not a roof. So, we worked with our structural engineers to ensure the old steel could handle the new wind loads with the canopy. And every truss was curved differently, and probably hand-done, so we had to make templates of each and make custom steel bracketry to conform.
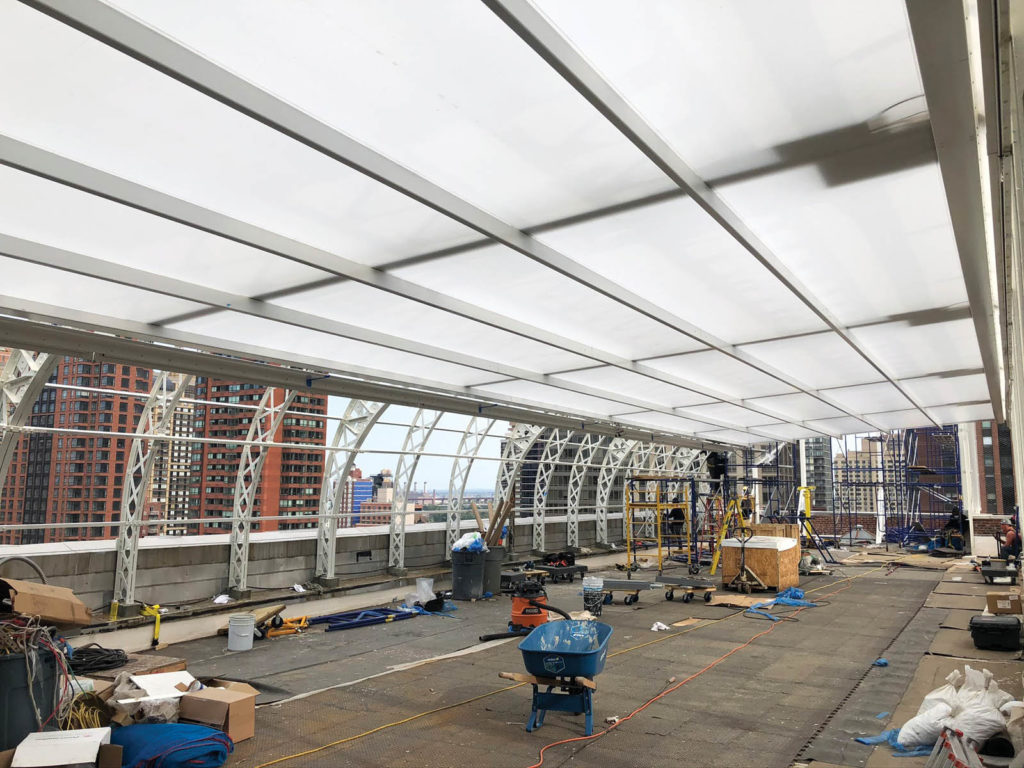
What were the unique, challenging and complex facets?
1. The roof site was on a busy street. We had to hoist building materials through the existing trusswork, so everything had to be sized to fit the crane hoist.
2. This was during the height of the pandemic, so we were collaborating via Zoom calls just as everyone was learning to work from home.
3. We use a lot of custom aluminum extrusions in our product, and we ended up being short one important extrusion. We weren’t able to get it on time due to supply chain issues, so we had to take a different extrusion of ours and make modifications to sub it out for the missing one. Then we went back to our engineers for an analysis on the structural connections to make sure everything would work.
4. We completed fabrication in June of 2020, but the city was locked down so we weren’t able to get our technician in for installation until October 2020.
5. The city came back with an objection to the canopy, citing zoning laws that it would contribute to the floor area ration unless the fabric was more than 50% translucent. We searched worldwide to find that in a fabric with the right strength properties. Luckily, I discovered Seaman Corp. had just developed the new Shelter-Rite 3820 FRLTC DC-0 Clear fabric with 65% light transmission and strength characteristics suitable for use with the En-Fold retractable tensile canopy system. That was sheer luck since we were running out of time and options.
What skills and knowledge were most important to getting this done? Just the combined years of experience of myself and our design director, Steve Goecke. I’ve been with the company 21 years and have worked on big, retractable stadium roofs and all types of kinetic architectural elements, and lots of unique challenges in terms of design. Steve comes from a background mostly in building facades.
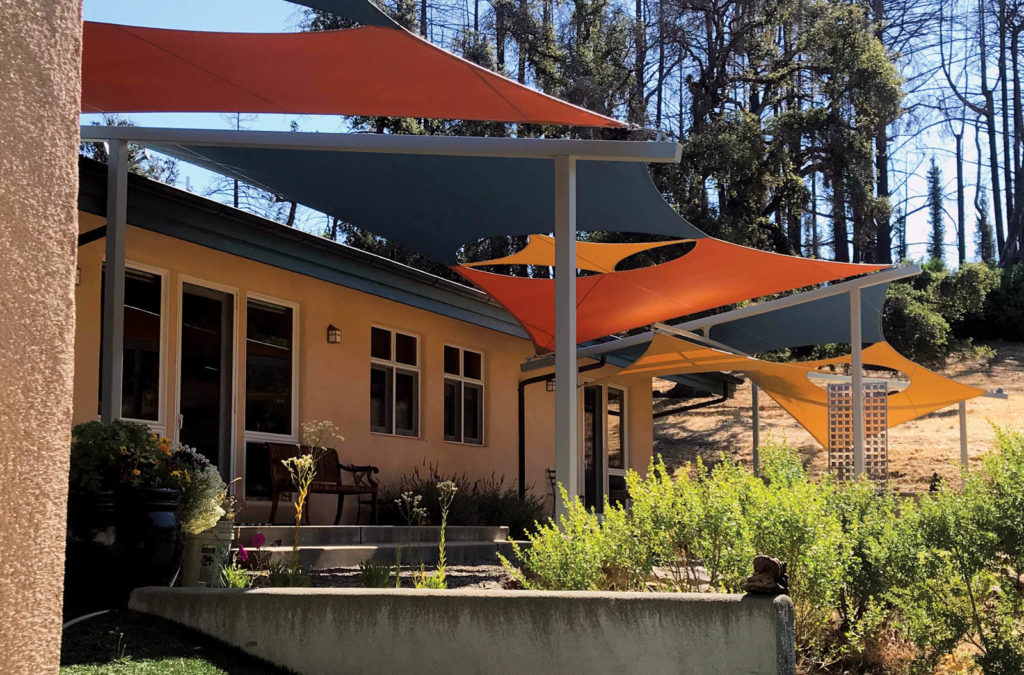
2021 Outstanding Achievement award
Tensioned Awnings and Canopies
GuildWorks LLC, Portland, Ore.
Interviewee: Mar C. Ricketts, Principal and founder
Project specs: The client wanted a multicolor, multipiece installation with a minimal frame structure that could provide summer shade on the southern side of her house. The piece had to work around an existing layout, which included a large metal sculpture. The primary challenge was creating a simple structure with minimal posts that could support the southern edge of the building without touching it, but fit tightly against the eave. That called for a multipiece tension fabric installation with good shaping on a minimal frame using Soltis 92 by Serge Ferrari.
How was this different from past projects? We’ve mostly moved out of the residential marketplace but had a relationship with this client through her business.
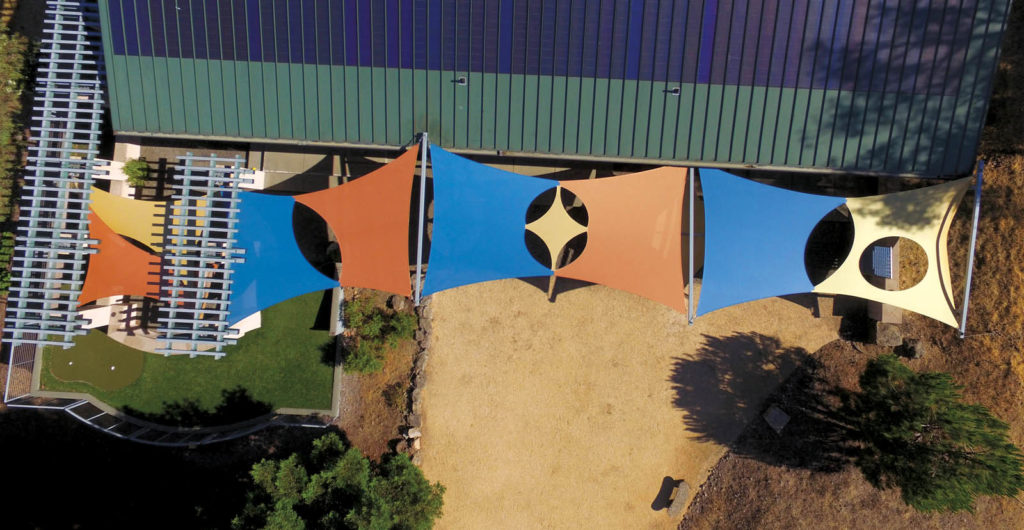
What were the unique, challenging and complex facets?
1. The client wanted multiple colors and multiple pieces in a pretty small space, something that would come only 10 to 12 feet off the house but include a lot of design expression.
2. Although the tension structure created sizable loads, we wanted to keep necessary details like hardware on the upside, away from the viewer.
3. We wanted this to look like it’s flying right out from the house, to duck over and under the roof line to interplay with the house in a designed transition.
4. The client has a 10-by-4-foot fine art piece coming up through a hole in the structure. During design we had to integrate, go around and hold space for that piece. We didn’t want the space to feel overly crowded, and we wanted to be able to see the piece clearly, so we created sight lines.
What skills and knowledge were most important to getting this done? Our VP and director of construction Sebastian Collet comes from an architecture background, and I come from architecture and engineering, so we brainstormed on design along with our team. Our in-house production facility tested and prototyped all details to make sure this would really work.
Advice for fabricators dealing with similar challenges? In earlier years, I was afraid I’d keep losing money by overseeing every stage of a project, but I’ve seen it pay off.
Michelle Miron is a freelance writer based in Hugo, Minn.