A fabric-clad tower in southern Germany brings technicians, elevator experts and the public together in one spectacular vertical setting.
By Bruce N. Wright, FAIA
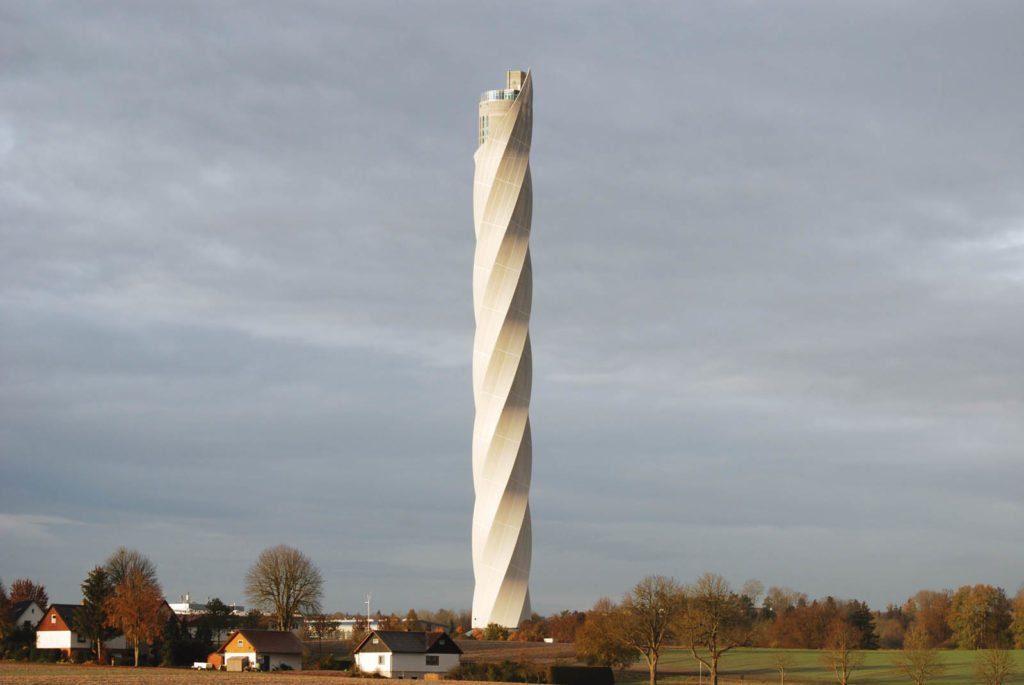
Paris’s Eiffel Tower, London’s Big Ben, China’s Three Pagodas, Iraq’s spiral minaret: Over time, all became more than just their function—they became iconic symbols of their location.
Likewise, ThyssenKrupp’s fabric-wrapped Rottweil test tower must become a symbol of its place and surroundings, says Helmut Jahn, FAIA, the internationally celebrated architect who collaborated with the equally celebrated structural engineer Werner Sobek on the tower. “It can do that if it does not just fulfill its function as a test facility for ThyssenKrupp, but [also] for the residents and visitors of this place,” he says.
ThyssenKrupp, located in Rottweil, Germany, is a leading world designer and manufacturer of advanced elevators, especially for very tall buildings. The city of Rottweil, established more than 2,000 years ago, is bisected by the valley of the Neckar River in the southwest corner of Germany and is shaped by 14th- and 15th-century Gothic style churches and historic stone defense towers that encircle the inner core. With its fabric mesh that acts as a shield to protect the structure from intense sunlight and wind, the ThyssenKrupp tower is in dialog with these ancient towers.
“Designing a building of such importance is a serious responsibility,” Jahn says. “The tower becomes an expression of the progressive culture of ThyssenKrupp and of the progressive spirit of the citizens of Rottweil.”
Genius loci
It makes sense that this fabric-clad tower is located here. Rottweil is almost equidistant between two historically significant cities linked to the development of fabric/membrane structures and its industry: south of Rottweil is Radolfzell (located at the northwestern end of the inland “sea” of Lake Constance, which shares borders with Austria, Switzerland and Germany). This is where a number of membrane structure fabricators have located as well as engineering and design firms specializing in tension structures. Farther north is Stuttgart, where the University of Stuttgart has a history of training dozens of innovative structure engineers since the 1940s, and where the progenitor of all this activity, Frei Otto, established his Institute for Lightweight Structures (IL). Many important architects and engineers have passed through these institutions on their way to creating new and influential firms.
“The ThyssenKrupp tower is used to test and certify high-speed elevators,” Sobek says, “and contributes considerably toward reducing the development time of future skyscrapers throughout the world.”
With 12 elevator shafts, offices and meeting rooms within, and at the highest level, an observation deck for visitors (including exhibition space and a cafe), the tower is more than just a research and development building. It has multiple entrances located at different elevations at the base of the tower to accommodate different groups of people.
“The building entrance is integrated into the landscape by means of berms,” Jahn says. “A ring-shaped bypass opens up four different entrances that allow customers, employees, visitors and delivery traffic to be separated. Parking spaces for cars, buses and trucks are located parallel with the bypass.”
In sequence, starting from the top: at 246 meters (807 feet) high, the tower is the tallest structure in the valley, and one of the tallest in Germany. Visitors get 360-degree views of the Alps and immediate area at the 232-meter (761-foot) mark, the highest visitor platform anywhere in Germany. Areas for presentations and company offices are located on levels from 185 to 200 meters (607 to 656 feet), with magnificent views of Rottweil.
“Customers can access the lifts via a naturally lit, two-story lobby” at the base, Jahn says. “The glazed shafts show all the elevators, and a lightweight, glass staircase leads to the double-decker and twin elevators” on view and in use by visitors.
Concrete + fabric in harmony
The structure of the test tower is made of a thin reinforced concrete tube with a diameter of 20.8 meters (68 feet), with the walls of the elevator shafts inside the tube only marginally transferring horizontal loads throughout the height of the tower. This means that it is a highly efficient structure with an average exterior wall thickness of only 25cm (9.8 inches). Wind loads on the concrete shell add minimal deformations at the top of the tower of only 331mm (13 inches) resulting in a ratio of 1/725, a value comparable to the usual ratios in most high-rise construction.
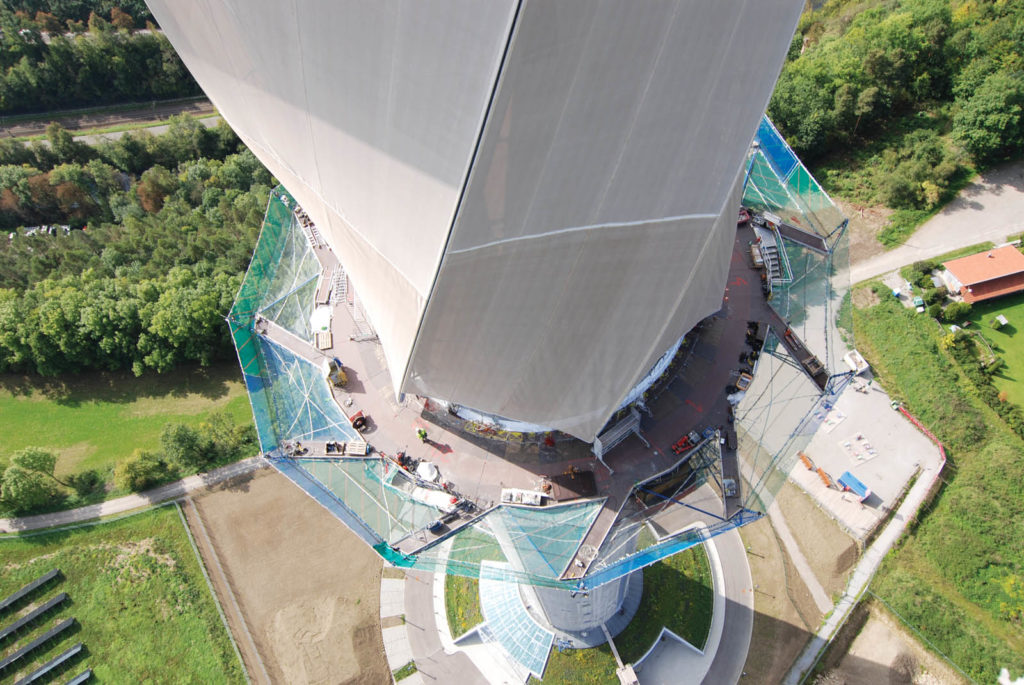
The exterior fabric wrap contributes to the overall structural performance and improves the durability of the concrete portion of the tower. “The envelope consists of an extremely long-lasting PTFE-coated glass fiber fabric that increases in transparency as it ascends the tower,” according to a report from Sobek’s office. Approximately 16,000 square meters (172,200 square feet) of the fabric membrane is installed in a helical pattern in six long strands of fabric—each strand 12 meters (39 feet) wide—weaving their way up the tower about 2.5 meters (8 feet) away from the concrete tube surface. Moving up the tower, the mesh fabric begins at the base with 15 percent openness; at about a quarter way up, 18 percent openness; at the halfway point, 22 percent openness; to arrive at the top quarter of the total height with 27 percent openness, bringing in more light and expanding the views from the elevators as they rise to the observation deck level.
“The fabric is secured to six steel pipes that spiral around and encircle the shaft of the tower,” Sobek says. “The prestressing required for the fabric creates spatially curved surfaces between the pipe ribs … which has an extremely positive effect on the vibration behavior of the tower, and in particular dampens the effects of oscillations.”
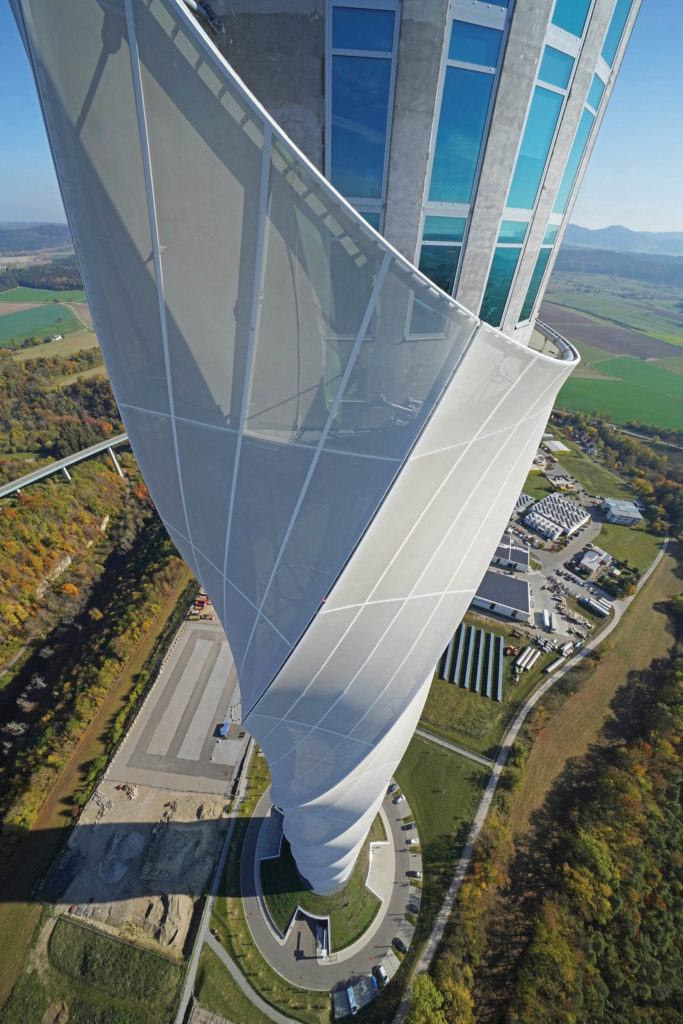
Complexity drives innovation
Constructing the fabric wrap for the tower posed numerous challenges to Taiyo Europe GmbH, the project engineer/project manager, as well as the lead installer of the PTFE glass membrane.
“The complexity and uniqueness of this project resulted from the height of the building,” says Frank Höreth, managing director for Taiyo Europe. “Due to the high altitude and continuous movement of the concrete tower caused by wind and sunlight, a special method of surveying was needed to develop the precise positioning of anchors” for attaching the helical steel pipes.
The local construction safety regulations also imposed on the process. Consequently, Taiyo Europe created a ring-shaped installation platform that moved up and down the tower. Installing and mounting the anchors began from the bottom, followed by attaching the six helical steel pipes and attachments for the fabric beginning from the top down. Some 1,150 anchor plates were affixed, and attached to these were steel A-beams that were used to hold the fabric away from the concrete tower surface by 2.5 meters (8 feet).
Award winning and sustainable
Architects are always trying to find more value in their designs that give back to the client, and energy savings are a big part of all construction worldwide by mandate for obvious reasons. When efficiency can be combined with good aesthetics, everyone wins.
“Sustainably, the concrete mass is used as energy storage,” says Jahn, where any “existing waste heat is used to condition the rooms.” This strategy of finding secondary and sometimes tertiary means of ringing every last BTU out of the energy consumed by buildings is more and more the norm for architectural and construction practice.
The ThyssenKrupp tower was given the Balthasar Neumann Award for 2018, a prize that is awarded to a team for outstanding achievements in integral planning. The award highlights how different disciplines have cooperated “in an exemplary and innovative manner and far exceeding established engineering standards to construct a building.” In the same year, the tower earned the German Federal Engineering Award and was a finalist for the German Facade Award. More recently, the tower received the 2019 Award of Excellence in the Hybrid Tension Structure category of IFAI’s International Achievement Awards (IAA) and earned the IAA “Best in Category” title for all fabric structure projects.
Precedent-setting in both structural and honorary fields, the ThyssenKrupp tower is a success socially for its observation deck: in its first year of operation, more than 250,000 visitors enjoyed great views of the Alps and surrounding valley.
“The monumentality of this tower,” Jahn says, “is evident both day and night by the light. Sculptural and dematerialized, the tower becomes a true landmark.”
Bruce N. Wright, FAIA, is an architect and consultant to architects, as well as a senior instructor at Dunwoody College of Technology. He is a frequent contributor to Specialty Fabrics Review and Advanced Textiles Source.
SIDEBAR: Project data
Client: ThyssenKrupp, Rottweil, Germany
Architects: Werner Sobek with Helmut Jahn, FAIA
Architecture firm: JAHN
Structure and membrane design: Werner Sobek
Fabrication: Flontex.eu Membrane Structures
Contractor: Ed. Züblin AG
Project Engineer/Management/Installation: Taiyo Europe GmbH
Fabric: PTFE-coated glass mesh (multiple transparencies), Verseidag-Indutex GmbH