The great urban critic Jane Jacobs—known for her highly influential and transformative 1961 book The Death and Life of Great American Cities—noted that there are many repeatable factors that can determine the success of public spaces, not the least being that any neighborhood could be deemed welcoming (hence successful and alive) if it includes aspects of each of her “Four Pillars of Effective City Neighborhood Planning.” The fourth pillar includes a checklist of essentials: “parks, squares, and public buildings to attract people,” which can then lead to delightful and vibrant spaces.
All subsequent consultants of public space design and development, and in many cases private space design as well, are indebted to Jacobs and to her mentor William H. Whyte, who expanded the tool kit of public space design while working for the New York City Planning Commission. Whyte’s 1980 book The Social Life of Small Urban Spaces closely observed (through time-lapse photography and direct questionnaires with people) that “good public spaces had many people in them, and that what attracts people most is other people.” Whyte enumerated a list of key elements: “trees, food, sitting, water, sun, streets” and what he called “triangulation”; i.e., a combination of all these elements that adds up to more than the sum of their parts.
This article presents three case studies of inviting projects, both private and public, that use these elements, with the addition of fabric structures, to demonstrate the value of creating “delightful and vibrant spaces.” Each of these projects takes advantage of fabric’s flexibility and economy in shaping beautiful and attractive venues. Using fabric contributes to what the national design group Project for Public Spaces (PPS) calls “placemaking.” According to PPS, “Placemaking facilitates creative patterns of use, paying particular attention to the physical, cultural and social identities that define a place and support its ongoing evolution.” I’m sure that Jacobs and Whyte would approve of these projects.
Miller Lite®House
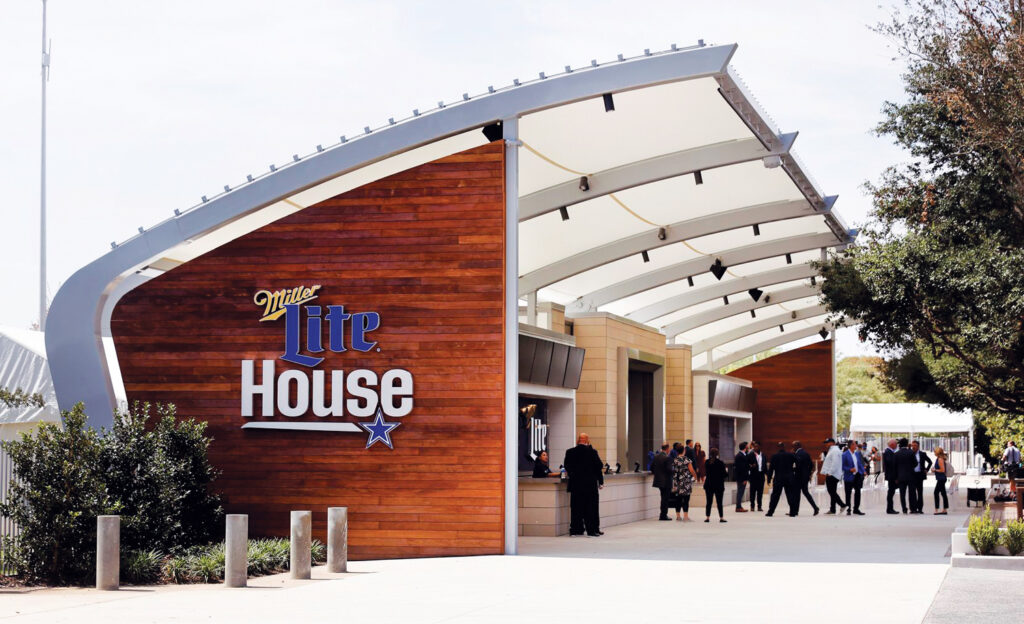
Anyone who has experienced a Dallas Cowboys game in person knows that only half of the total scene at AT&T Stadium in Arlington, Texas, is on the field. In fact, if you were to arrive at the new Miller Lite®House pre/postgame venue, it’s possible that the actual football game might be an afterthought. American football over the years has developed numerous traditions, including tailgating (usually out in the parking lot, if you’re lucky to get a spot close to the gate).
At AT&T Stadium, every square foot of space inside and out has been monetized and the guests seem to love it at all price points. With the Lite®House, located at the west end of the stadium, smaller groups of spectators than would be found inside the main arena can find a stage for music and entertainment, a 70-yard turf football field (for field games) flanked on both sides by two beer gardens with tree-covered groves and seating (for up to 650 fans), four video boards, and two fantasy football walls. According to the sponsorship web page, this venue can entertain up to 3,000 guests.
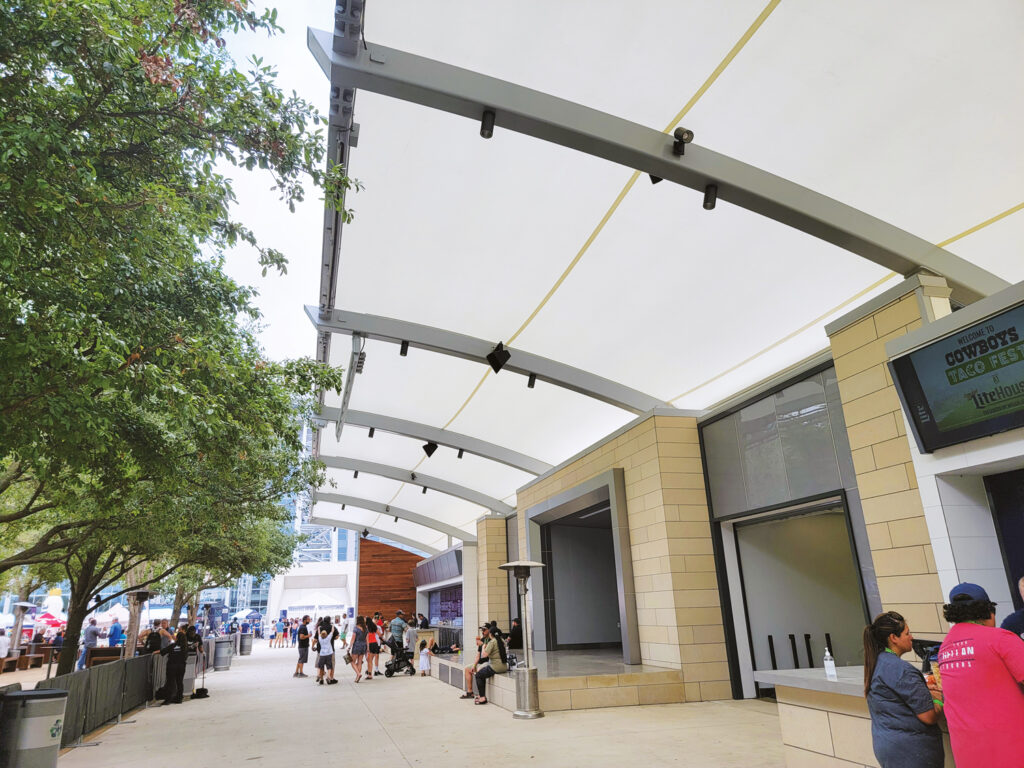
The Lite®House utilizes a fabric structure canopy as its main physical feature. A bow-curved fabric shade reaches out toward the turf, softening the daylight and extending far enough to protect most of the area in front. Architects HKS Inc. and general contractor Manhattan Construction, who built the original AT&T Stadium in 2010, again teamed up on this project. Design, engineering, fabrication and installation of the fabric canopy was done by the Texas office of Enclos Tensile Structures (ETS). “The most difficult part of the fabrication,” says Phillip Finzer, director of construction at ETS, “was the architecturally exposed structural steel at the two ends of the building.”
Eight bow arches in a row are supported at the back by bringing the arch down to the ground footings and propping these up with vertical columns placed about one-fourth of the total arch distance from the back edge, creating seven bays of fabric. The result is a spectacular soaring light canopy—light both visually and in weight. The two ends have infill wood walls that extend the support columns forward to near center of the bow arches, framing the ensemble like bookends. “These were large, built-up members,” says Finzer, “with a lot of welding. Minimizing the warpage was the name of the game here.” The Lite®House has proven to be a very welcoming space that completes the west end of AT&T Stadium.
Project data: Dallas Miller Lite®House
Client: Dallas Cowboys
Architect: HKS Inc.
Structural engineering: Walter P Moore
Fabric structure: Enclos Tensile Structures
General Contractor: Manhattan Construction
Fabric: PTFE, white
Photos: Phil Finzer
PQ: “The most difficult part of the fabrication was the architecturally exposed structural steel at the two ends of the building.” Phillip Finzer, Enclos Tensile Structures
Green School New Zealand
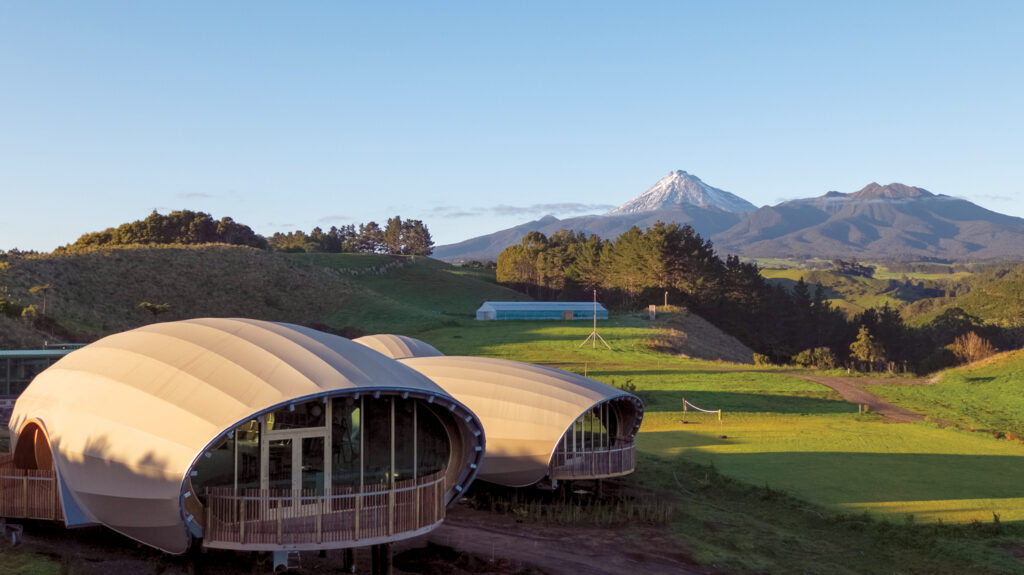
An eco-friendly campus in Taranaki, New Zealand, Green School New Zealand incorporates sustainable materials, natural ventilation and highly efficient systems to make a near-zero carbon impact. Although not technically a public space, this school is part of a network of schools whose mission is to nurture “green” leaders who will take the sustainability message to the global community and create more sustainable spaces in both public and private spheres.
Green School New Zealand bases its pedagogical foundation on respect for the local nature, the landscape and mana whenua (“land rights” in the indigenous Maori language). The school’s core principle of sustainability is at the center of both the curriculum and the campus design.
The influential British/Australian architect Glenn Murcutt is known for his iconic design philosophy “touch the Earth lightly,” an ethos that is based on an Aboriginal proverb and that informs his practice with a commitment to sustainable design in the Australian environment.
A first phase of the Green School New Zealand classroom structures—three pod-like enclosures lifted up from the ground “with the lightest of touches to the earth,” states the architect’s project sheet—was completed in May 2020. These wakas are playfully placed on the land of a defunct farm.
“The classrooms’ smooth organic forms set [our] challenge to rethink traditional building methods,” according to press materials from BOON Ltd., a national award-winning architectural design practice located in New Plymouth, New Zealand. “Consideration has been given to longevity of the buildings and how they function sustainably in the varied west coast weather context.”
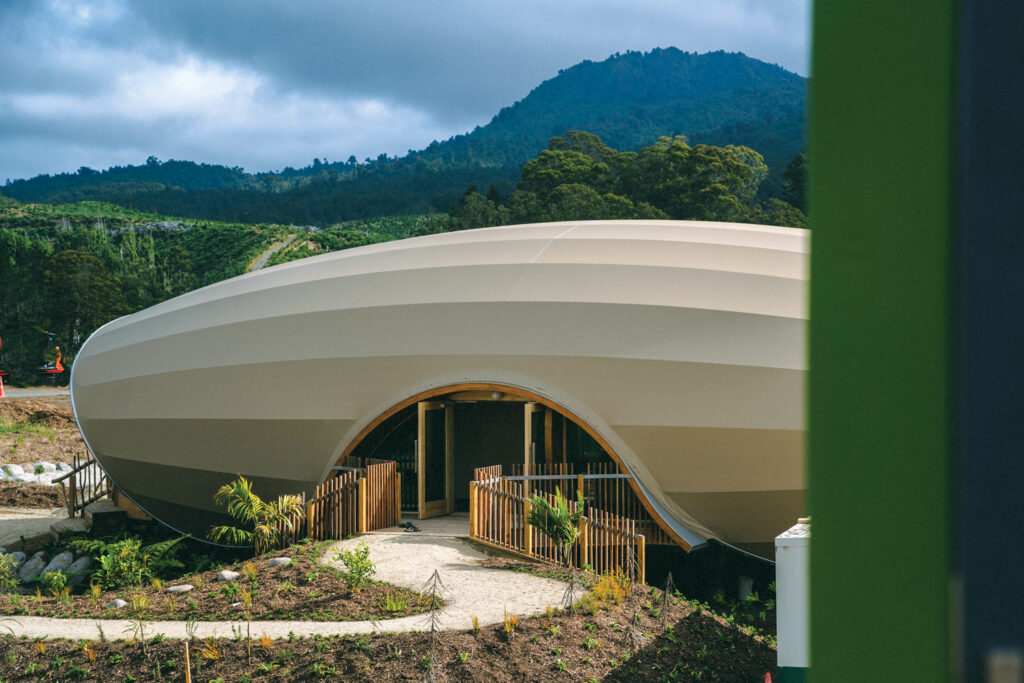
The design uses passive measures throughout the buildings, making the most of cross ventilation, and each pod is clad in an earth-colored membrane to reduce heat gain. High-level layered insulation, vapor barriers and under-floor heating systems keep the wakas at a constant temperature.
Fabric Structures Ltd. was contracted to design the membrane and steel substructures that form the turtle shell-like roofing. The company also fabricated and installed both steel framing and membrane cladding. “We were approached by the architect and worked with them to ensure their concept would work,” says James Bunn, project manager on the Green School. “The overall complexity to the project was the shape involved and construction materials used.” Glulam engineered timber beams are the main shaping structural supports. Steel spacing rails between inner ply skin and the exterior fabric pull the cladding tight to the beams.
“The glulam beams created large tolerances on-site, requiring the steel to be custom fit to each of the three structures,” says Bunn. “3D digitizing was used to design and construct the membranes. The high stretch of the fabric, paired with the shape of the structures, added the additional complexity of staged tensioning over multiple weeks.”
The finished project won a 2020 Western Architecture Award from the New Zealand Institute of Architects. Fabric Structures also secured the contract for a second phase that was completed in late 2022.
Project data: Green School New Zealand
Client: Green School New Zealand
Architect: BOON Ltd.
Project management: Fabric Structures Ltd., Meco Engineering
Engineering: Fabspan, Fabric Structures Ltd., Palmer Canvas Ltd.
Fabric used: PVC, VALMEX® lodge de lux FR by Mehler Texnologies
Photos: Fabric Structures NZ
PQ: “The high stretch of the fabric, paired with the shape of the structures, added the additional complexity of staged tensioning over multiple weeks.” James Bunn, Fabric Structures Ltd.
Mountain Health Arena
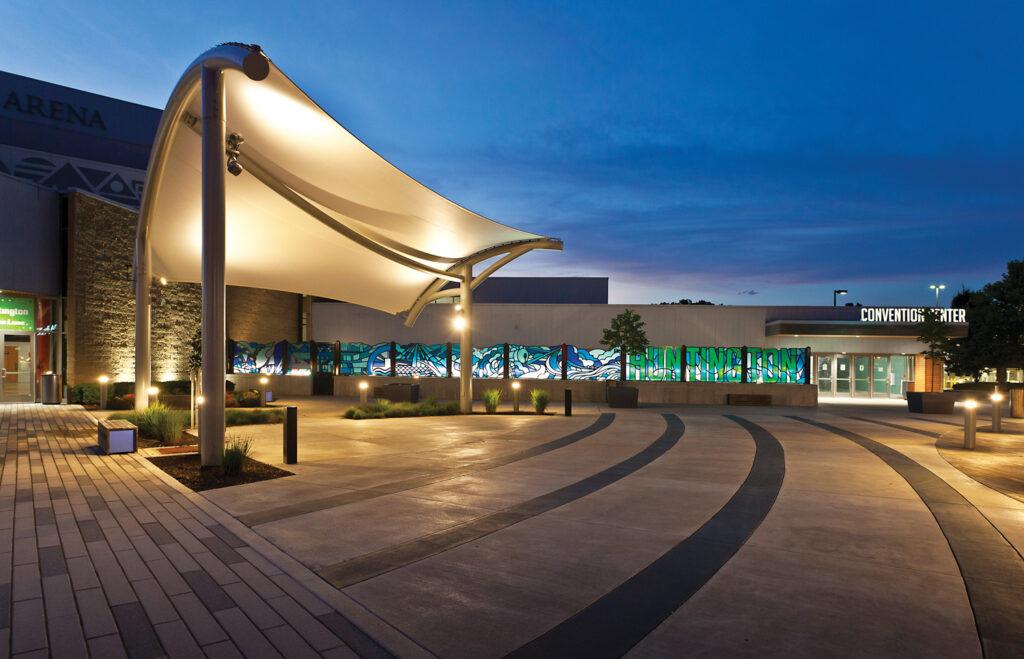
The city of Huntington, W.Va., was in the process of updating Mountain Health Arena, its civic arena and convention center, through a series of phased renovations. The arena’s general manager, Cindy Collins, noticed that the “sea of concrete” that fronted the facility was a missed opportunity to engage the community. It was clear that if the prominent downtown corner was to be a gathering space for the community, a plan to convert the hostile entryway into an urban oasis was needed.
Edward Tucker Architects, the architects of record for the rejuvenation of the arena, called upon GAI Consultants Inc. and its Community Solutions Group to develop a proposal for rethinking the arena and convention center’s hardscape entryway. The design team included CMTA as electrical consultants and Fountain Technologies as water feature designers. The collaboration illustrated that creative ideas could “soften the hardscape and create space for fun and exciting experiences,” says Phoebe Patton Randolph, principal with Edward Tucker Architects.
The group’s recommendations included adding an interactive water feature (a bubbling fountain placed in the center), open spaces with built-in seating and fire pits, and a covered, sculptural tensile fabric stage structure that became the new focus for the entire project.
Framing the backdrop is a custom-designed screen wall that mimics stained glass and incorporates designs representing local landmarks. The design team worked with 3D modeling to study the form, sight lines and scale of the fabric structure in relation to the landscaping.
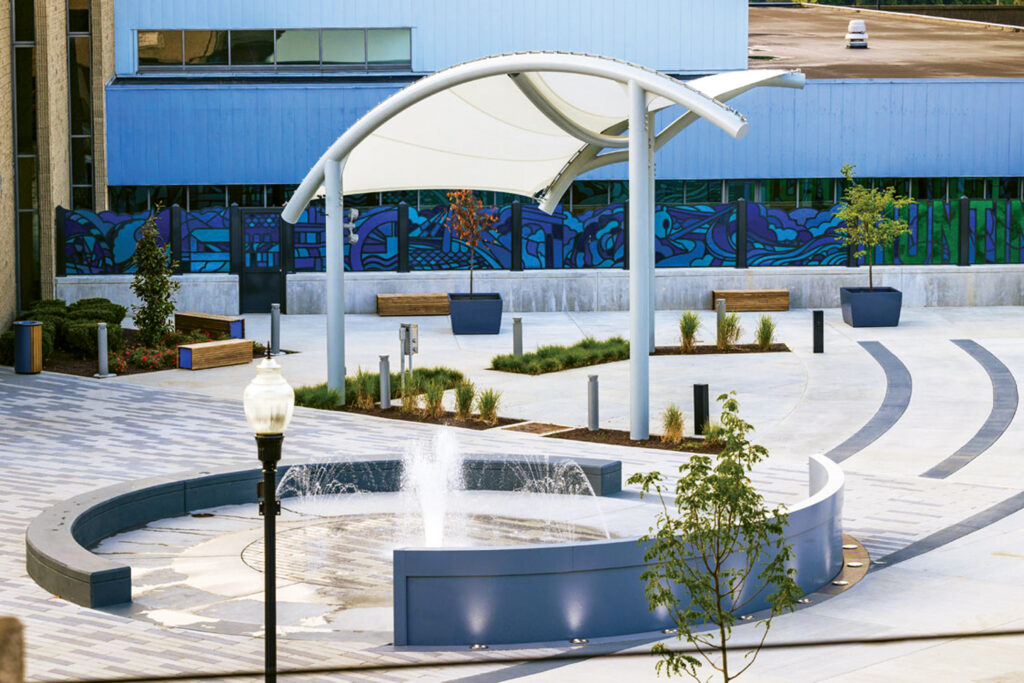
Eide Industries Inc., which had previously completed a successful tension structure in nearby Charleston with GAI, worked closely with the design team to evaluate the design and detail of the tensile fabric shade structure. The company also developed detailed working drawings and assisted with its fabrication and installation. “We liked the idea of the fabric shape because it tied nicely in with the water feature and the playful design concept,” says Randolph. “The curves of the structure and the [new] softscape were complementary.”
“A white PTFE membrane was used for the trapezoid shade cover, which measures approximately 26 feet by 33 feet by 44 feet by 17 feet,” says Angela Juarez, project lead for Eide’s tensile division. “The height dimensions range from 9 feet to 20 feet, and the assembly [fabric and metal structure] was engineered for 115 mph wind loads.”
The complete transformation of this plaza shows how welcoming a public space can be if all the elements are working together.
Bruce N. Wright, FAIA, is the former editor of Fabric Architecture magazine and teaches architecture and construction management at Dunwoody College of Technology in Minneapolis, Minn.
Project data: Mountain Health Arena
Client: City of Huntington, W.Va.
Architect: Edward Tucker Architects
General Contractor: GAI Community Solutions Group
Fabric structure: Eide Industries Inc.
Engineering: Eide Industries Inc.
Consultants: CMTA, Fountain Technologies
Fabric used: PTFE, SHEERFILL® V (white) by Saint-Gobain Performance Plastics
PQ: “The fabric shape tied nicely in with the water feature and the playful design concept. The curves of the structure and the [new] softscape were complementary.” Phoebe Patton Randolph, Edward Tucker Architects.